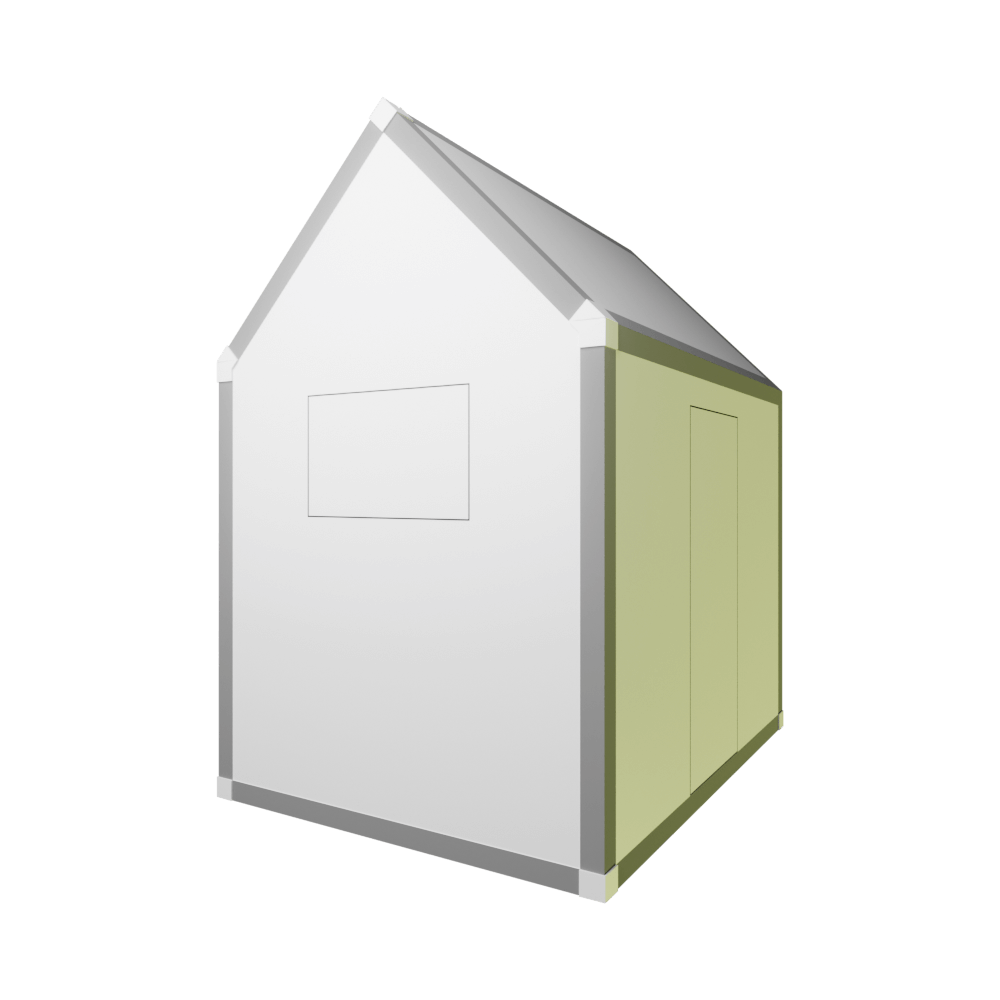
Inside the BOXX
BOXXED composite panels offers a range of high-quality foam which are sustainable in both product and manufacturing.
The rPET and EPS foams are an ideal choice for building green. Offering numerous environmental advantages including reduced energy consumption, provide excellent thermal performance, lead the alternative core materials in emissions savings, both contribute to the circular economy, and both are produced in Canada reducing the carbon footprint and environmental impact of our panels.
Our panels are versatile and can be used for a variety of applications. We offer customizable options such as size, thicknesses, to help our clients find the perfect product for their specific needs.
Fiberglass Structural Tubes & Chases
At Boxxed, we’ve moved away from using traditional construction methods in favour of new technological advances to maximize our products lifespan and your investment. Utilizing fiberglass structural tubes is the smart alternative to wood, steel and aluminum framing. Our FRP structural tubes are non-conductive – thermally and electrically, do not rust, corrode, warp, rot, decay or attract insect damage.
Benefits
- Corrosion resistant
- High in strength
- Lightweight – weighs 80% less then steel
- Fire-retardant
- Low in maintenance
- Non-conductivity – thermally & electrically
- Dimensionally stable
- Non-magnetic
- Consistent
- Easy to install
- No hazardous materials
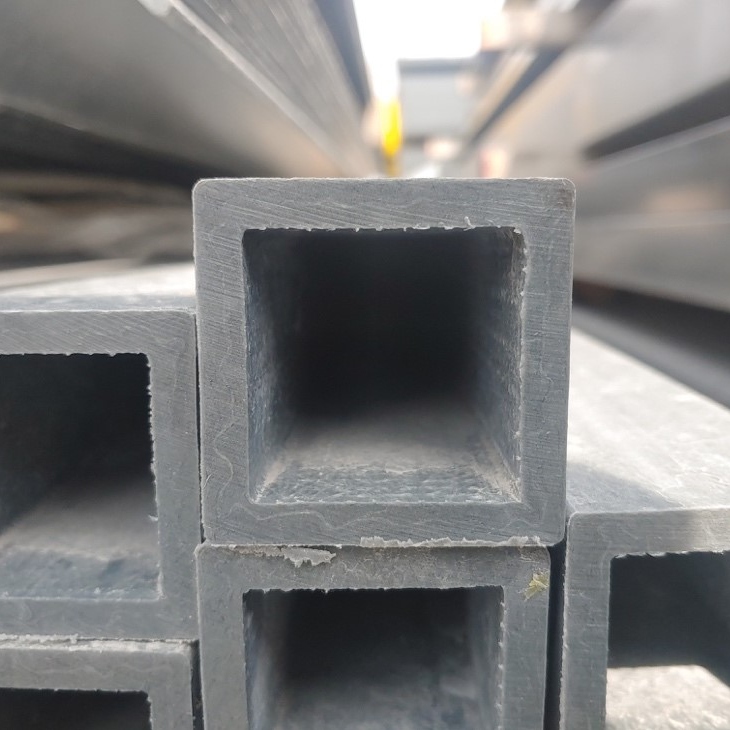
glued not screwed
At BOXXED, we use a structural adhesive which has been reviewed and approved for use in Canada and the USA. The governing bodies mandate this to ensure products meet environmental initiatives and health safety laws.
Why glue and not screws? Imagine a screw (or fastener) penetrating a surface, the hole created could potentially lead to an ingress point for water to penetrate the envelope leading to a weakening of the system, structural failure due to corrosion and ultimately water damage to the panels. We eliminate the use of all fasteners and only use glue to improve the structural integrity and lifespan of our products.
A structural adhesive can be defined as a load-bearing material with high modulus and strength that can transmit stress without loss of structural integrity. Structural adhesives can replace welding, bolts, screws, rivets, and other traditional attachments in a wide variety of applications.
To name a few, structural adhesives are used in the aircrafts, trains, buses, building industries, etc. The adhesive we chose is suitable for structural joints that are subjected to dynamic stresses.
glue benefits
- One-component silane-terminated polymer-based technology
- Ageing- and weathering-resistant
- Bonds well to a wide variety of substrates
- Capable of withstanding high dynamic stresses
- Can be over-painted
- Non-corrosive; high electrical resistance
- Low odour; low VOC content and solvent-free
- Silicone- and PVC-free
- UV Resistent
rPET - from bottle to foam
recycled Polyethylene Terephthalate (rPET) insulation is made entirely from recycled plastic beverage bottles.
rPET insulation has a high fatigue resistance, excellent thermal stability, low thermal conductivity over the lifespan. Lightweight and strong makes it possible to build lighter and maximise payload, prevents degradation by moisture, rodents, and insects, and has excellent screw retention.
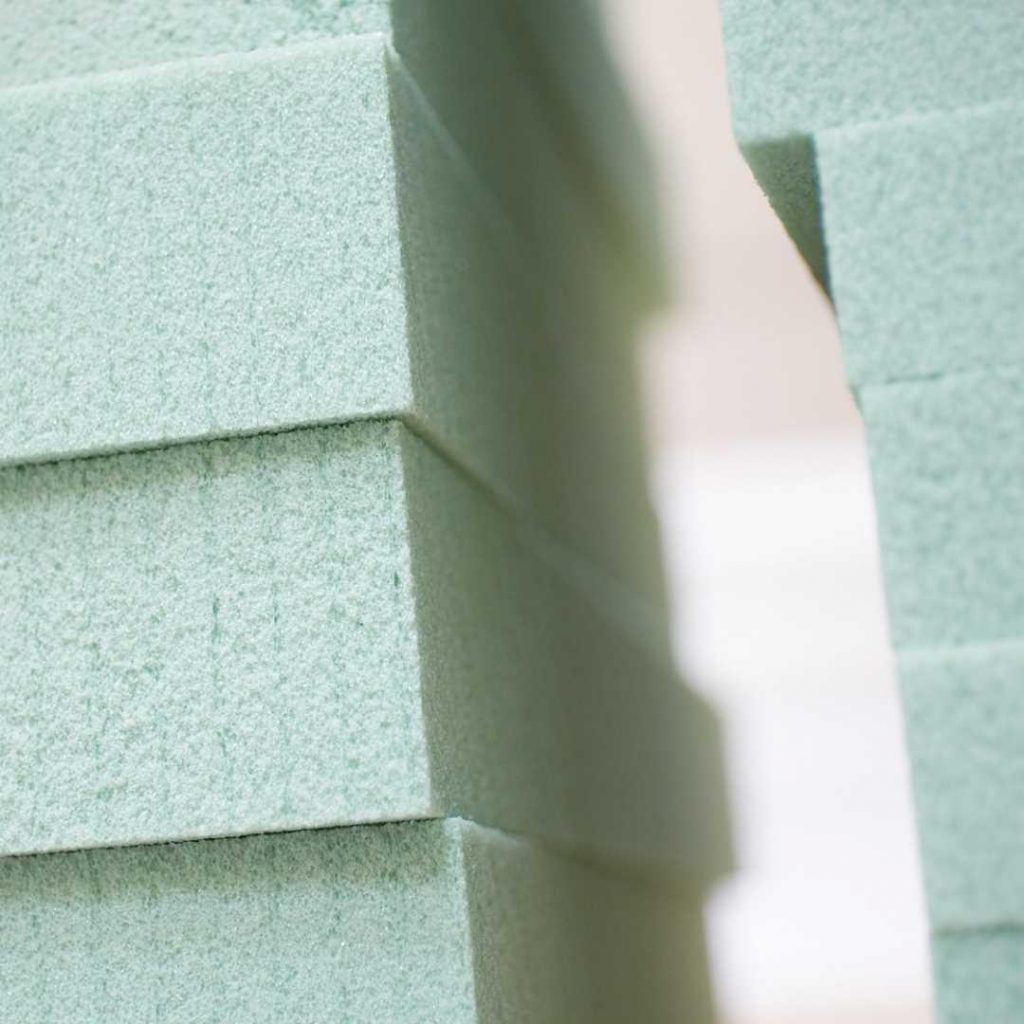
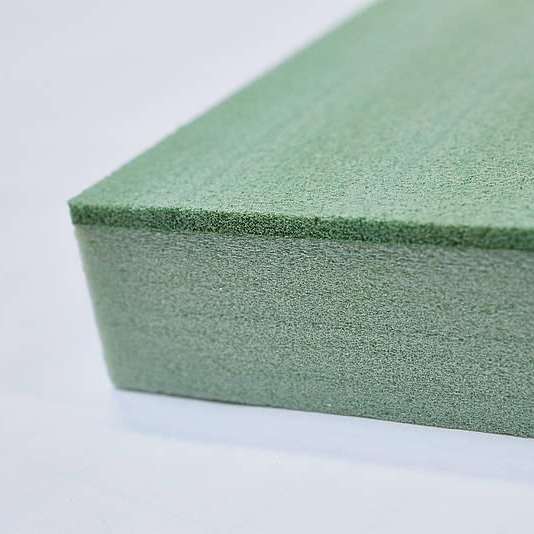
rPET benefits
- Water Resistant
- Fire Resistant
- Mold Resistant
- Impact Resistant
- Durable
- Eco-friendly
- 100% recycled material
- Soundproofing properties
- Energy efficient
- Excellent fatigue properties
- R-value 2” = R8.47
- Closed cell insulation

closing the loop
The impact of plastic on our ecosystem is undisputed. Every second more than 16,000 plastic bottles are sold worldwide. Less than 50% of these bottles are collected for recycling, and only 7% go to make new PET bottles. Most plastic bottles end up in a landfill or our environment, where plastic takes hundreds of years to decompose.
Instead of ending up in landfills or oceans PET materials (plastic bottles) are collected, cleaned, sorted and crushed into flakes. This is followed by a granulation process and finally extrusion foaming. After the product has reached its life expectancy, rPET is entirely 100% recyclable.
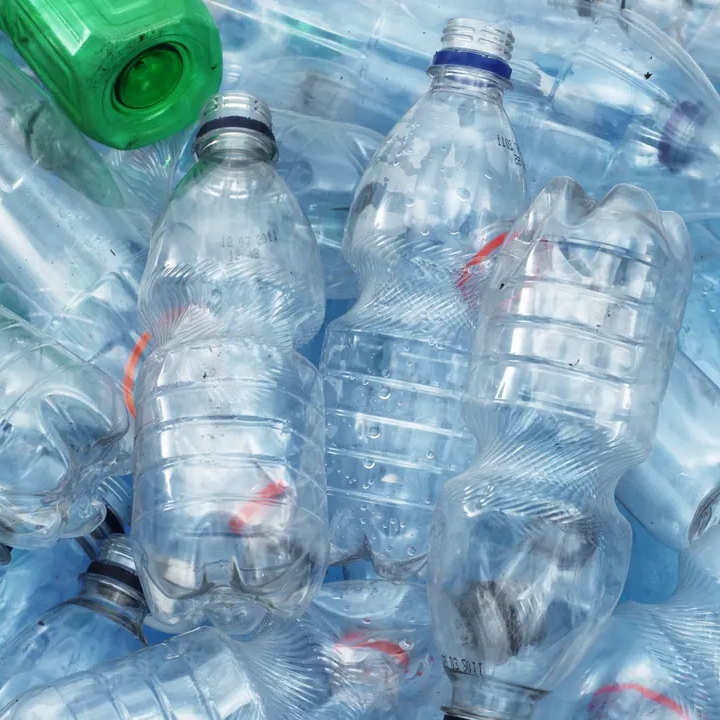
how many plastic bottles are you going save?
EPS – full of hot air
Expanded polystyrene (EPS) insulation is an inert closed cell foam plastic which is 98% air and commonly used in residential and commercial industries.
EPS insulation is made from polystyrene beads that are expanded using hot air, inflating the beads with air up to 40 times bigger. The expanded beads are fused together with steam molding them into a block resulting in a lightweight and durable foam material.
EPS insulation has excellent resistance to freeze/thaw, zero capillary, low moisture absorption and zero off gassing and zero loss of R-value overtime. Another amazing characteristic is more effective at lower temperatures, R-value increases as temperatures decrease.
Additionally, EPS does not contain chlorofluorocarbon (CFC’s), hydrofluorocarbon (HFC’s) or hydrochlorofluorocarbon (HCFC’s) blowing agents. EPS contains air, is safe and easily recyclable, will never rot, or support mold or mildew.
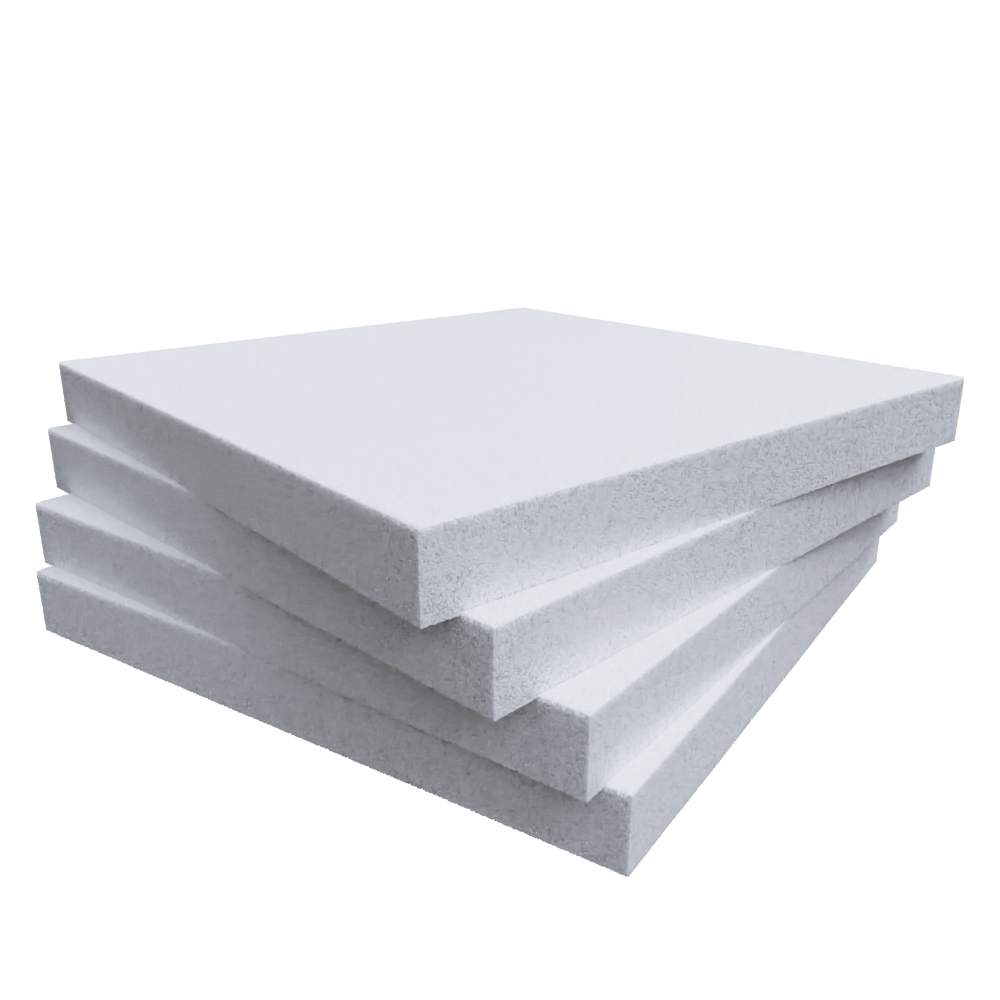
EPS benefits
- Water resistant
- Mold resistant
- Impact resistant
- 100% recyclable
- Sustainable (one material)
- Energy efficient
- R-value 2” = R9.35
- Closed cell structure
Outside the BOXX
BOXXED composite panels offers a variety of corners to choose from including fiberglass pultrusion’s, aluminum extrusions and angles for their sustainability and recyclability.
BOXXED composite panels are designed and built to be continuous and lap at the corners keeping the effective R-value consistent. To achieve this, Boxxed uses structural corners which are thermal bridge free. Imagine, no condensation or heat loss?
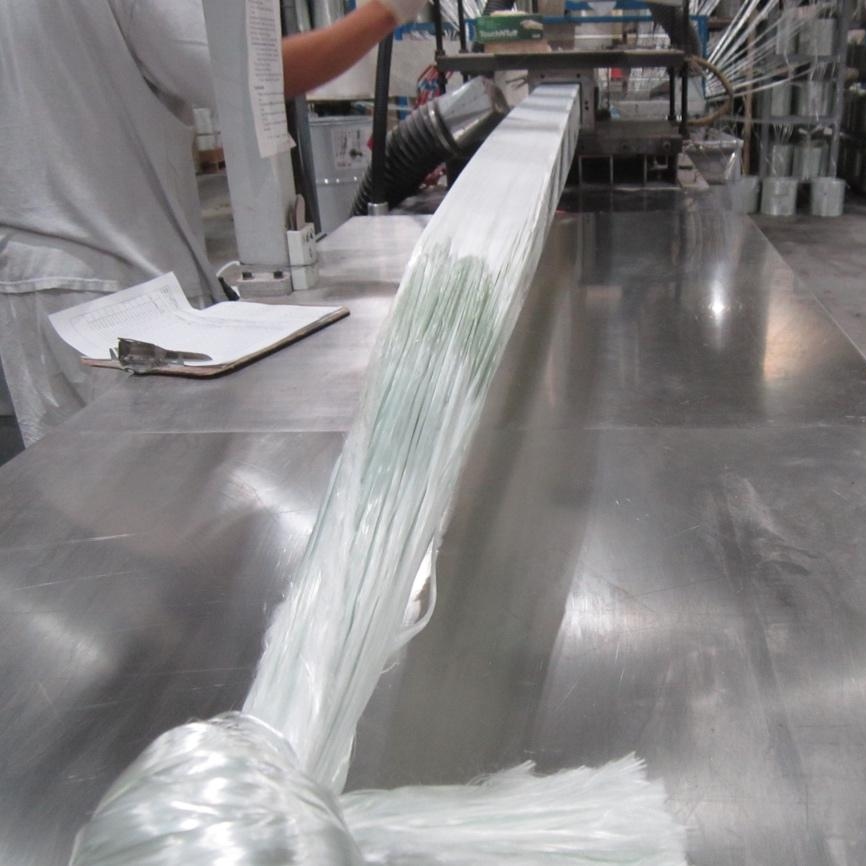
BOXXED fiberglass pultrusion’s
BOXXED composite panels patent pending fiberglass pultrusion’s is a new innovative structural corner securing panels and eliminating thermal bridging at the joints where the panels meet.
The novel fiberglass structural corner is made by a pultruded process and is not extruded. The pultrusion method is where continuous fiberglass strands are mixed with a proprietary blend of resin and “pulled” through a custom die to create a consistent profile.
The fiberglass pultrusion has properties which are lightweight, corrosion resistant and high tensile strength. The fiberglass has superb resistance to thermal conduction, expansion and contraction making them ideal for use the mobile industries harsh environments while eliminating build-up of condensation.
The key benefit of using a fiberglass pultrusion and fiberglass panel together is they have a low coefficient of thermal expansion and contraction properties reducing movement, maintaining an excellent seal and longevity of the products.
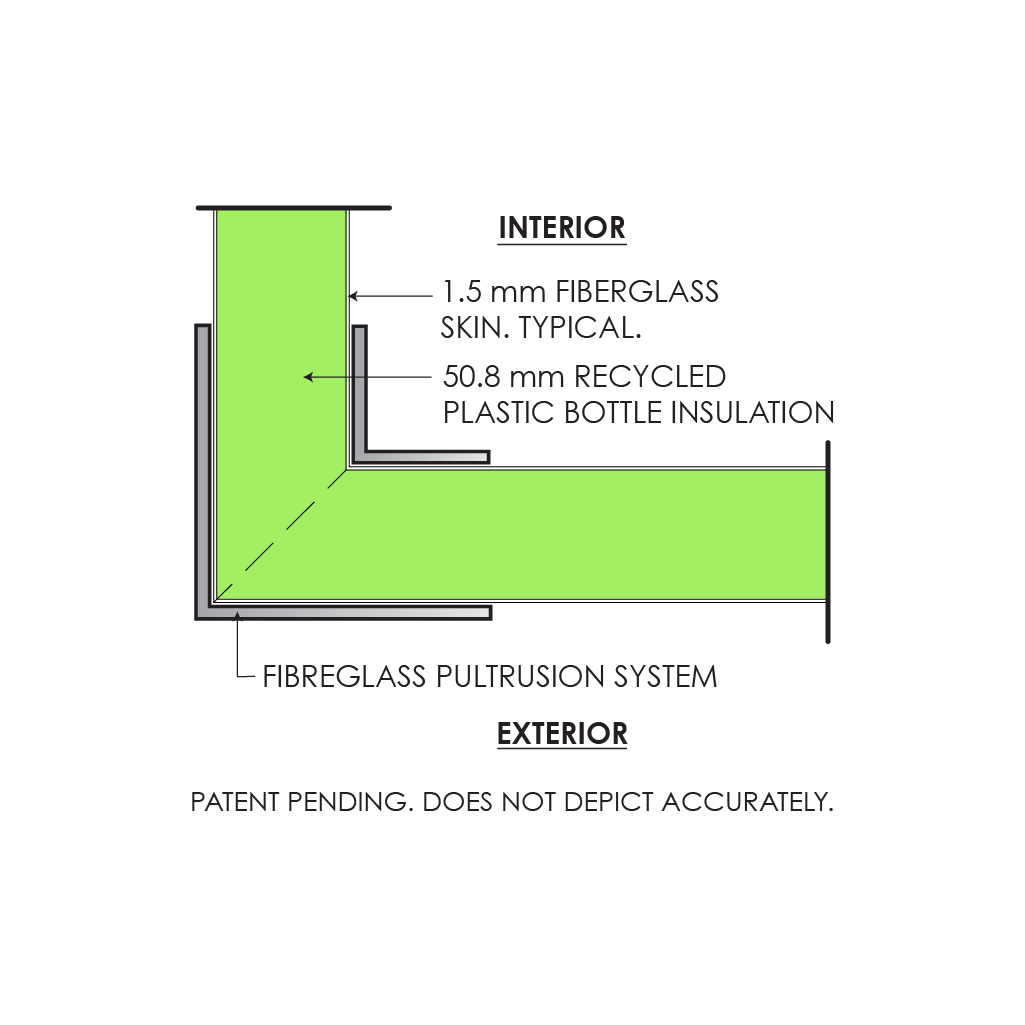
fiberglass pultrusion’s
Our Boxxed fiberglass pultrusion’s are paired with our core eco boxx for an easy to assemble system. The pultrusion’s come in 45 and 90 degree options and allow for a 54mm total thick composite panel.
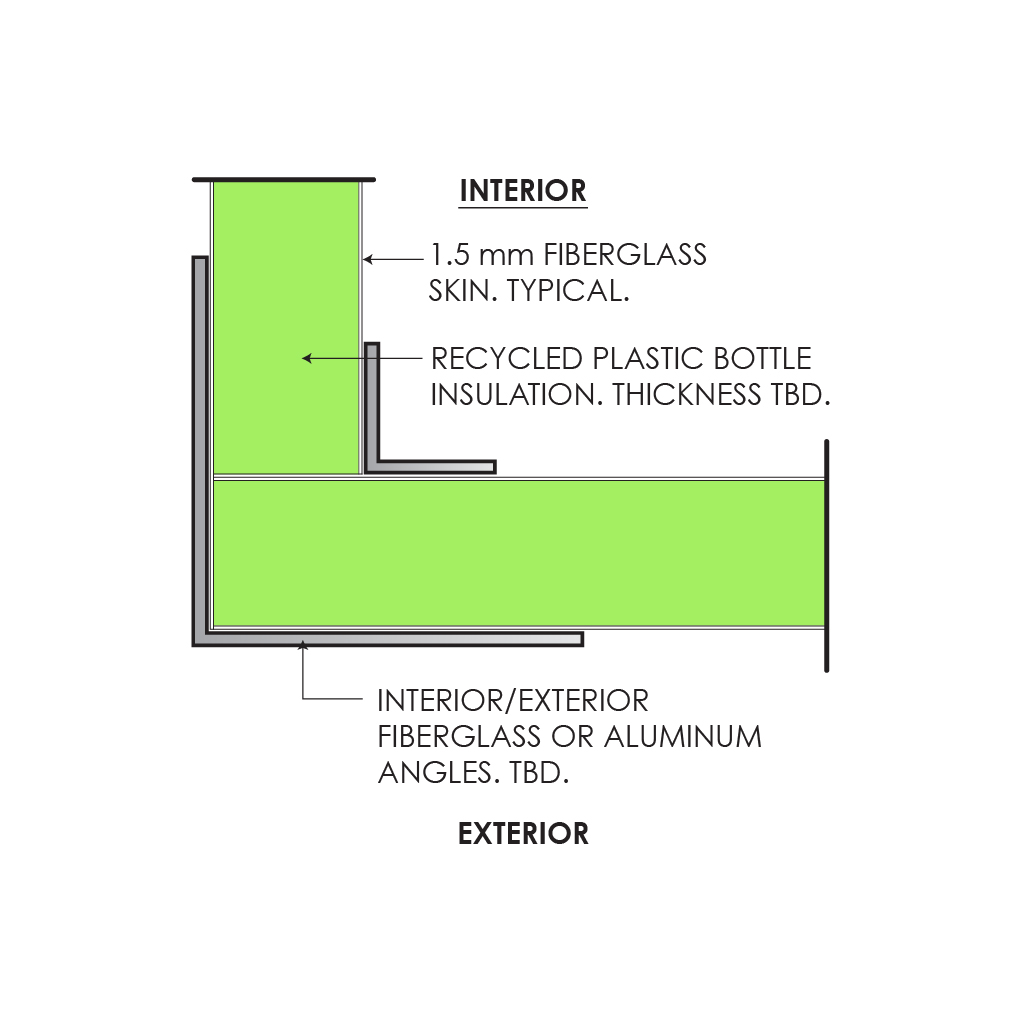
aluminum and fiberglass angles
For those who are looking for a custom thicker eco composite panels for greater r-value, we offer both aluminum and fiberglass angles.
Tried and true, aluminum angles are a consistent choice and reliable option used for decades in many industries.
Aluminum and fiberglass angles provide strength and stability to the corners, ensuring a secure and long-lasting installation.